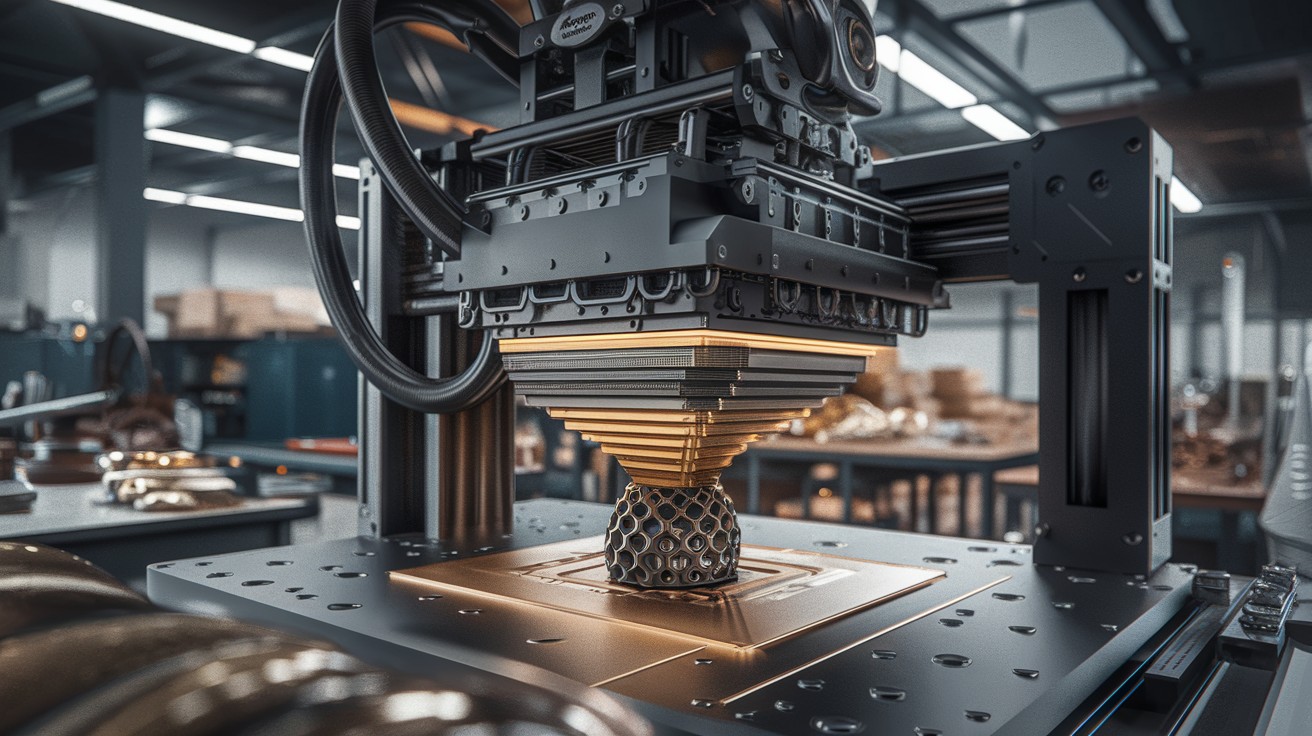
Fabrication Additive Métallique : Une Révolution à Portée
Imaginez un monde où les usines ne gaspillent plus de matériaux, où les pièces métalliques complexes naissent d’une simple superposition de couches, et où les petites entreprises rivalisent avec les géants industriels grâce à une technologie accessible. Ce n’est pas une utopie, mais une réalité qui se dessine avec la **fabrication additive métallique (FAM)**. Pourtant, malgré ses promesses alléchantes – réduction des coûts, personnalisation à l’extrême, diminution des déchets – cette innovation peine à s’imposer largement, surtout auprès des TPE et PME. Pourquoi ce paradoxe ? Entre défis techniques, besoins en compétences et coûts initiaux, plongeons dans les enjeux qui façonnent l’avenir de cette révolution industrielle.
La Fabrication Additive : Une Opportunité Sous-Exploité
La fabrication additive, souvent appelée impression 3D, n’est plus une nouveauté réservée aux laboratoires de recherche. Aujourd’hui, elle s’invite dans les ateliers, portée par des procédés comme le **WAAM (Wire Arc Additive Manufacturing)** ou les traitements thermiques au laser. Mais si ses avantages sont évidents, son adoption reste timide. Les grandes entreprises, avec leurs budgets conséquents, explorent déjà ces horizons, tandis que les petites structures, cœur battant de l’économie, hésitent encore. Les raisons ? Des barrières techniques et organisationnelles qui demandent à être surmontées.
Les Promesses d’une Technologie Transformative
Pourquoi tant d’engouement autour de la FAM ? Parce qu’elle redéfinit les règles de la production. En superposant des couches de métal, elle permet de créer des pièces sur mesure sans les pertes massives des méthodes traditionnelles. Moins de déchets, donc une empreinte écologique réduite. Plus de flexibilité, donc une capacité à répondre aux besoins spécifiques des clients. Mais ce n’est pas tout : elle ouvre aussi la porte à la **fonctionnalisation des matériaux**, un concept qui consiste à doter les pièces de propriétés uniques, comme une résistance accrue ou une légèreté optimisée.
« Les opportunités de la fabrication additive sont bien réelles : elle réduit les coûts et les déchets tout en permettant une créativité sans précédent. »
– Lionel Buissières, chargé de projets chez EuraMaterials
Ces atouts séduisent, mais ils ne suffisent pas à convaincre tout le monde. Pour beaucoup de PME, le passage à l’acte reste freiné par des obstacles concrets, qu’il s’agisse d’investissements initiaux ou d’un manque de savoir-faire. Alors, comment transformer ces promesses en réalités tangibles ?
Les Défis Techniques : Le Casse-Tête du Post-Traitement
Si la fabrication additive impressionne par sa capacité à modeler le métal couche par couche, elle ne livre pas des pièces prêtes à l’emploi. Le **post-traitement** devient alors un enjeu central. Prenons le cas du traitement thermique : il ne s’agit pas d’une simple formalité, mais d’une étape décisive pour garantir la solidité et la durabilité des pièces. Les microstructures formées pendant l’impression, influencées par les variations de température, peuvent fragiliser le produit final si elles ne sont pas maîtrisées.
Olivier Dellea, chercheur au CEA Hauts-de-France, éclaire ce point : les cycles thermiques rapides, comme ceux induits par un laser, permettent de raffiner les grains du métal, améliorant ainsi ses propriétés mécaniques. Mais cela exige des équipements coûteux et une expertise pointue, deux ressources souvent hors de portée des petites entreprises. Résultat ? Une technologie prometteuse reste sous-exploitée faute d’accessibilité.
Sustain-3D : Une Initiative pour Démocratiser la FAM
Face à ces défis, des acteurs se mobilisent. C’est le cas de **Sustain-3D**, un projet européen lancé en mai 2024, qui réunit des partenaires danois, belges, néerlandais et français. Porté en France par EuraMaterials, ce programme ambitionne de lever les verrous qui bloquent l’adoption de la FAM. Comment ? En créant une communauté d’experts – industriels, chercheurs, fablabs – pour partager connaissances et solutions.
Lors d’une rencontre organisée en octobre dernier à l’ENSAM de Lille, les participants ont exploré les problématiques du post-traitement. Lionel Buissières, impliqué dans le projet, explique : « Nous voulons répondre aux besoins concrets des industriels, en leur offrant des outils pour surmonter les obstacles techniques et logistiques. » Une démarche collaborative qui pourrait changer la donne pour les PME.
WAAM : Quand le Soudage Réinvente la Production
Parmi les procédés de la FAM, le **WAAM** se distingue par son approche ingénieuse. En s’inspirant du soudage, il dépose des cordons de métal successifs pour construire une pièce en trois dimensions. Mais ce qui le rend unique, c’est sa capacité à intégrer le traitement thermique dès la fabrication. Adrien Van Gorp, maître de conférences à l’ENSAM, détaille : « Les cordons réchauffent les couches précédentes, provoquant un recuit naturel qui peut être contrôlé pour obtenir les propriétés voulues. »
Cette optimisation réduit le besoin de post-traitement, un avantage majeur pour les industriels soucieux de leurs coûts et délais. Dans des secteurs comme l’aéronautique, où chaque pièce doit répondre à des normes strictes, cette approche pourrait révolutionner la chaîne de production. Mais encore faut-il que les entreprises maîtrisent ce savoir-faire.
Coût et Délais : L’Équation à Résoudre
Adopter la FAM, c’est aussi jongler avec une équation économique complexe. Les machines coûtent cher, les matériaux ne sont pas donnés, et les étapes finales – retrait des supports, usinage, contrôles – demandent du temps. Sébastien Eyrignoux, chef de projet chez Lisi Aerospace, souligne l’importance d’optimiser ces phases pour rester compétitif. « Chaque minute gagnée en production, c’est un avantage sur le marché », affirme-t-il lors de la rencontre Sustain-3D.
Pour les PME, cette pression est encore plus forte. Sans les ressources des grands groupes, elles doivent trouver des solutions astucieuses, comme mutualiser des équipements ou s’appuyer sur des réseaux comme Sustain-3D. Une chose est sûre : réduire les coûts et les délais reste un défi clé pour rendre la FAM incontournable.
Compétences et Formation : Le Nerf de la Guerre
Une machine, aussi perfectionnée soit-elle, ne vaut rien sans les compétences pour la faire fonctionner. Avec la FAM, les besoins en formation explosent. Comprendre les subtilités des microstructures, maîtriser les logiciels de conception, piloter les procédés de post-traitement : autant de savoir-faire qui manquent encore cruellement dans les petites structures. Les universités et centres de formation, comme l’ENSAM, jouent un rôle crucial, mais l’effort doit être collectif.
Sustain-3D l’a bien compris. En réunissant industriels et académiques, le projet favorise le transfert de connaissances. Mais cela prendra du temps. En attendant, les PME doivent souvent se débrouiller seules, freinant leur transition vers cette technologie d’avenir.
Un Avenir à Construire Ensemble
La fabrication additive métallique n’est pas qu’une prouesse technique : elle incarne une vision de l’industrie de demain, plus agile, plus durable, plus inclusive. Pourtant, son destin dépend de notre capacité à lever ses freins. Voici quelques pistes pour y parvenir :
- Rendre les équipements plus accessibles via des financements ou des partenariats.
- Multiplier les formations courtes adaptées aux besoins des PME.
- Développer des réseaux collaboratifs comme Sustain-3D pour partager les bonnes pratiques.
Le chemin est encore long, mais les initiatives se multiplient. À l’image d’EuraMaterials et de ses partenaires, l’industrie française a les cartes en main pour faire de la FAM un levier de compétitivité. Reste à transformer l’essai.
Les PME au Cœur de la Révolution
Si les grandes entreprises dominent souvent les récits d’innovation, ce sont les PME qui pourraient tirer le plus grand parti de la FAM. Leur agilité, leur proximité avec les clients et leur capacité à innover vite en font des candidates idéales. Mais pour cela, elles ont besoin de soutien – financier, technique, humain. Sustain-3D montre la voie, en fédérant une communauté prête à relever ces défis collectivement.
Alors, la fabrication additive métallique est-elle la clé d’une industrie plus forte et durable ? Sans doute, à condition que chacun – entreprises, chercheurs, pouvoirs publics – joue son rôle. L’avenir se fabrique aujourd’hui, et il commence dans les ateliers des petites structures prêtes à oser.