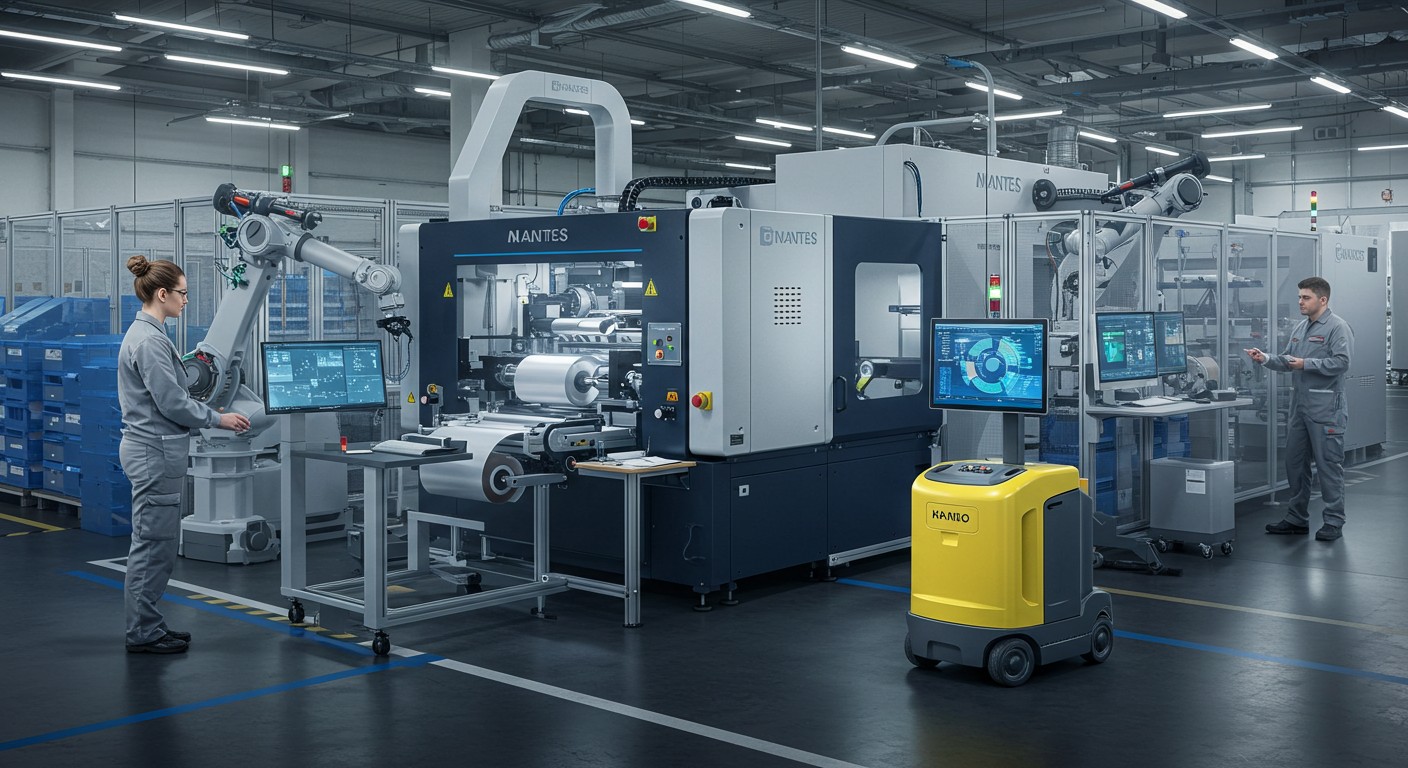
Automatisation : Armor Révolutionne l’Usine
Imaginez une usine où les machines dictent le rythme, où les opérateurs, libérés des tâches les plus pénibles, pilotent des technologies de pointe. À Nantes, l’entreprise Armor, leader mondial des rubans à transfert thermique, redéfinit le travail industriel grâce à l’automatisation. Mais cette révolution, qui promet confort et efficacité, soulève aussi des questions : comment les ouvriers vivent-ils cette transformation ? Plongeons dans les coulisses d’une usine qui fabrique le futur.
Armor : Pionnier de l’Industrie 4.0
Dans la région nantaise, l’usine d’Armor à La Chevrolière incarne une vision audacieuse de l’industrie 4.0. Depuis 2006, ce site de 60 000 m², spécialisé dans la production de rubans pour l’impression d’étiquettes et de codes-barres, s’est engagé dans une modernisation massive. Chaque année, l’entreprise investit 14 millions d’euros pour intégrer des technologies avancées, comme des systèmes automatisés de broyage ou des machines à grande vitesse. En 2019, cette ambition a été récompensée par le label Vitrine industrie du futur, une reconnaissance de son rôle de précurseur.
Mais au-delà des chiffres, c’est une transformation profonde du travail qui se joue. Les ouvriers, autrefois confrontés à des tâches manuelles répétitives, collaborent désormais avec des machines intelligentes. Cette évolution, bien que spectaculaire, n’est pas sans défis, notamment pour ceux qui doivent s’adapter à un rythme accéléré et à une solitude nouvelle dans les ateliers automatisés.
Une Salle de Broyage Réinventée
Entrons dans la salle BS2, inaugurée en 2024, où les matériaux pour les encres sont broyés avec une précision chirurgicale. Ici, tout est pensé pour minimiser l’effort humain et maximiser la sécurité. Un opérateur place un sac de pigments près d’une trémie, et un système de ventouses prend le relais, soulevant des charges pouvant atteindre 15 kg. Les solvants et pigments sont ensuite aspirés et transférés automatiquement dans une broyeuse, réduisant l’exposition des ouvriers aux produits chimiques.
« On ne sent plus les solvants, c’est plus aéré, moins étriqué. »
– Cyrille Pouvreau, opérateur chez Armor-Iimak
Le contraste avec la salle historique de broyage, encore en activité, est frappant. Dans cette dernière, l’odeur âcre des solvants persiste, et les opérateurs versent manuellement les matériaux, exposés à des risques d’inhalation. La salle BS2, avec ses écrans tactiles permettant de lancer des « recettes » de fabrication, incarne un bond vers l’avenir. Mais ce confort a un coût : les opérateurs, autrefois en équipe, travaillent désormais seuls, ce qui peut engendrer une certaine nostalgie de la convivialité passée.
La Machine Grande Vitesse : Un Colosse de Métal
Dans l’atelier d’enduction, la star est la MGV4, une machine à grande vitesse inaugurée en 2024 pour un investissement de 10 millions d’euros. Capable de traiter une bobine de film de 27 kilomètres à une vitesse de 1 km par minute, elle représente 60 % de l’activité de l’usine. Les opérateurs, formés pendant huit semaines, chargent des bobines Jumbo, qui sont ensuite encrées et séchées avant d’être enroulées à nouveau. Ce monstre technologique symbolise l’ambition d’Armor : réduire les coûts de production pour maintenir ses effectifs en France.
Cette machine illustre parfaitement l’équilibre entre innovation et défis humains. Si elle améliore la sécurité – un opérateur, victime d’un accident en 2018, témoigne d’une réelle avancée –, elle impose aussi une cadence infernale. La production a presque doublé par rapport aux modèles précédents, augmentant la pression sur les équipes.
« La cadence a quasiment doublé, entraînant un surcroît d’activité et davantage de pression. »
– Sébastien Héas, opérateur et délégué CGT
L’Humain au Cœur de l’Automatisation
L’automatisation ne se limite pas aux machines. Elle redéfinit aussi le rôle des ouvriers. Dans l’atelier de découpe et de conditionnement, où 40 % des effectifs sont des femmes, les cellules robotisées ont éliminé le port de charges lourdes. Noémie Fourrage, manager depuis quatre ans, souligne cette avancée :
« Les cellules robotisées ont éliminé le port de charges lourdes, lors du chargement des boîtes sur les palettes. »
– Noémie Fourrage, manager chez Armor
Pourtant, la mise en carton reste manuelle, une tâche répétitive souvent réalisée par des femmes. Armor prévoit d’automatiser ce processus d’ici trois ans, mais en attendant, les ouvrières doivent s’adapter au rythme imposé par les machines. Cette transition illustre un paradoxe : si l’automatisation soulage physiquement, elle peut aussi intensifier la pression psychologique.
Les Bénéfices et les Défis de l’Industrie 4.0
L’automatisation chez Armor offre des avantages indéniables. Voici les principaux bénéfices observés :
- Amélioration de la sécurité : Réduction des risques d’inhalation de produits chimiques et des accidents liés aux charges lourdes.
- Confort accru : Espaces de travail plus aérés et moins contraignants physiquement.
- Efficacité productive : Machines comme la MGV4 permettent de réduire les coûts tout en maintenant la compétitivité en France.
Cependant, ces avancées s’accompagnent de défis. La solitude des opérateurs en salle automatisée, la perte de convivialité et l’intensification des cadences sont des réalités auxquelles l’entreprise doit répondre. Pour Melvin Carnot, chef d’équipe, l’automatisation est une opportunité, mais elle nécessite un accompagnement humain :
« Tout se faisait au chronomètre avant. Aujourd’hui, il faut apprendre à piloter les machines et à s’adapter à leur rythme. »
– Melvin Carnot, chef d’équipe chez Armor-Iimak
Vers une Usine du Futur
Armor ne s’arrête pas là. L’entreprise envisage d’automatiser davantage, notamment dans la mise en carton, d’ici 2028. Cette ambition s’inscrit dans une stratégie globale de relocalisation industrielle et de compétitivité. En investissant massivement, Armor prouve qu’il est possible de conjuguer innovation technologique et préservation de l’emploi local. Mais pour réussir cette transition, l’entreprise devra écouter ses équipes et investir dans leur formation.
Le cas d’Armor illustre une tendance mondiale : l’usine intelligente redéfinit les métiers de l’industrie. Les opérateurs deviennent des pilotes de machines, les managers des stratèges de la transformation numérique. Pourtant, cette révolution ne doit pas oublier l’humain. Comment Armor parviendra-t-elle à concilier productivité et bien-être des salariés ? L’avenir nous le dira.
Un Modèle pour l’Industrie Française ?
L’expérience d’Armor à Nantes est un cas d’école pour l’industrie française. En misant sur l’automatisation, l’entreprise a non seulement optimisé sa production, mais aussi renforcé sa position sur le marché mondial des rubans thermiques. Voici un résumé des clés de son succès :
- Investissements constants : 14 millions d’euros par an pour moderniser l’usine.
- Formation des équipes : Huit semaines de formation pour piloter les machines complexes.
- Focus sur la sécurité : Réduction des risques grâce à des systèmes automatisés.
Ce modèle pourrait inspirer d’autres entreprises cherchant à allier innovation technologique et responsabilité sociale. Cependant, il faudra veiller à ne pas sacrifier le lien humain au profit de la productivité. L’automatisation est une chance, mais elle doit rester au service des travailleurs.
En conclusion, l’usine d’Armor à Nantes est bien plus qu’un site de production : c’est un laboratoire du futur industriel. Entre machines intelligentes et défis humains, elle trace la voie d’une industrie 4.0 où la technologie et l’humain doivent apprendre à coexister. Une chose est sûre : demain se fabrique aujourd’hui, et Armor en est la preuve vivante.