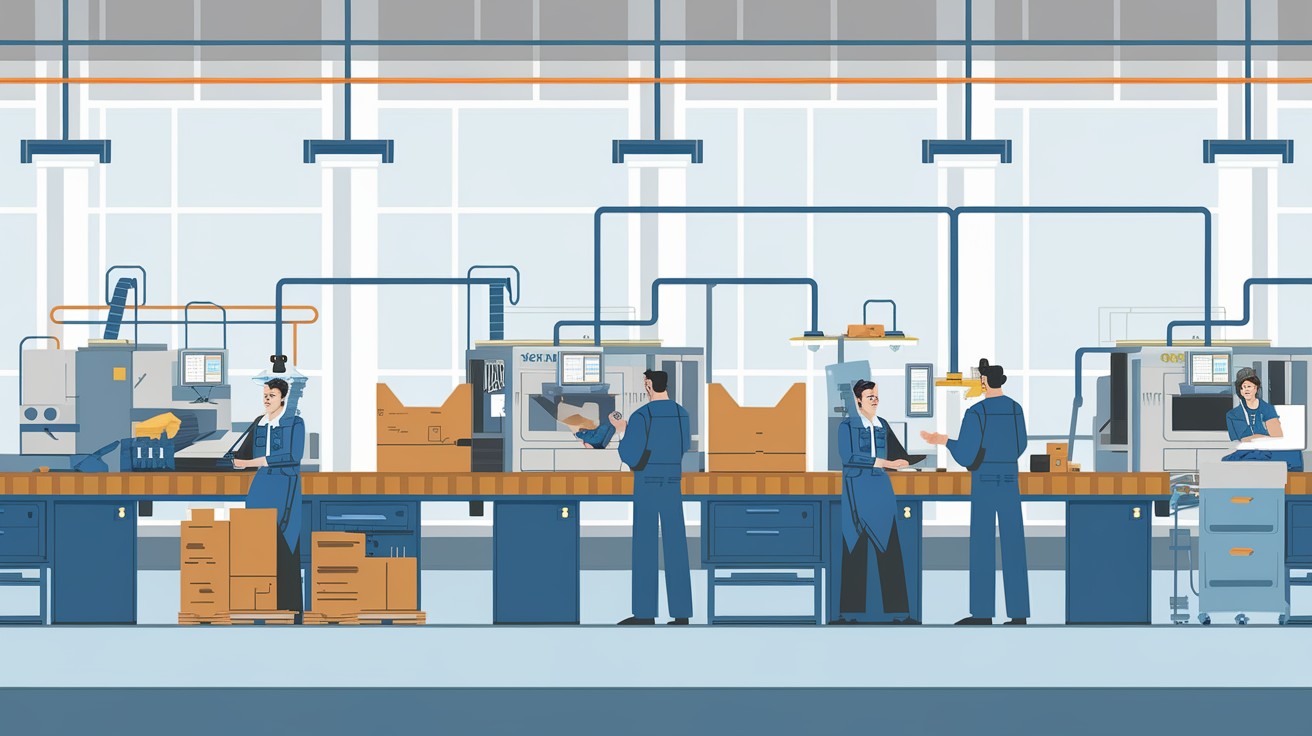
Bobst concilie coconception et standardisation à Bron
Dans l'industrie exigeante de l'emballage en carton ondulé, allier conception sur-mesure pour répondre aux besoins spécifiques des clients et standardisation des process pour gagner en efficacité est un véritable défi. C'est pourtant le pari relevé par Bobst, leader mondial des machines d'impression et de découpe, sur son site de Bron, dans la banlieue lyonnaise. Avec 650 salariés, il s'agit de la deuxième plus importante usine du groupe suisse.
Spécialisé dans les lignes pour l'impression et le façonnage de caisses, barquettes, boîtes et PLV en carton ondulé, le site est une véritable vitrine technologique. Les lignes d'assemblage les plus avancées, à l'image des Masterline, peuvent transformer jusqu'à 12000 feuilles par heure en associant impression flexo, découpe et collage dans un seul équipement pouvant mesurer jusqu'à 70 mètres de long.
Répondre sur-mesure aux demandes des clients
Si Bobst a fait le choix stratégique de conserver l'usinage des pièces les plus critiques en interne, comme les énormes cylindres servant de support aux clichés d'impression, l'essentiel des composants provient de fournisseurs spécialisés. La valeur ajoutée du site réside dans le co-développement avec les cartonniers pour concevoir des machines parfaitement adaptées à leurs besoins.
C'est un savoir-faire unique que nous avons su perpétuer. Beaucoup de nos concurrents savent façonner le carton, mais chez Bobst nous savons le faire avec une grande précision et à très grande vitesse.
– David Arnaud, directeur marketing produit
Les clients, de moins en moins nombreux mais toujours plus exigeants, attendent de la flexibilité et un service sur-mesure. Les lignes doivent pouvoir s'adapter facilement pour produire une grande variété de formats et intégrer les dernières innovations, par exemple en matière d'automatisation pour réduire les besoins de personnel qualifié, denrée rare dans le secteur.
Standardiser au maximum les process
Pour répondre à ces attentes tout en restant compétitif face à une concurrence asiatique et américaine montant en gamme, Bobst a réorganisé sa production selon les principes du lean manufacturing. L'objectif : réduire les délais en atteignant des standards de qualité élevés. Pour cela, le site est passé en flux tiré avec deux types de lignes d'assemblage :
- Des lignes "en flux" où la machine se déplace sur un rail, suivie par les monteurs
- Des îlots fixes dédiés aux commandes spécifiques où la machine reste en place
La méthode en flux est privilégiée car elle permet une plus grande standardisation des process, cruciale pour la rentabilité et la qualité. Les machines sont ensuite testées avant livraison au client.
Même si chaque ligne doit répondre à des demandes personnalisées, nous cherchons à rester le plus possible sur des modèles d'organisation standardisés. On parle de standards personnalisés.
– David Arnaud
Miser sur le service et la maintenance prédictive
Au-delà de la fabrication, Bobst mise sur les services associés pour se démarquer. Toutes les machines sont désormais connectées, ouvrant la voie à de nouvelles prestations comme le suivi des performances, la maintenance prédictive ou encore l'optimisation des réglages et consommations.
Un virage qui n'en est qu'à ses débuts dans l'ondulé mais qui constituera un atout concurrentiel clé pour convaincre des clients disposant souvent de machines ayant plus de 30 ans de franchir le pas de l'investissement. Bobst travaille donc main dans la main avec eux pour développer ces nouveaux outils d'analyse et d'optimisation.
Vers des partenariats renforcés avec les clients
Au final, le site de Bron illustre la mutation à l'œuvre chez un équipementier comme Bobst. Face à un marché de l'emballage en pleine transformation, il doit à la fois répondre à des demandes toujours plus spécifiques et être en mesure de les produire de façon standardisée pour rester compétitif. Un équilibre délicat qui passe par :
- Une collaboration étroite avec les clients dès la conception des machines
- Une organisation industrielle alliant flexibilité et standardisation
- Des services apportant de la valeur ajoutée tout au long de la vie des équipements
« Les clients ont besoin de nous et nous avons besoin d'eux » résume Hervé Simonin, directeur du site. Un modèle partenarial renforcé qui préfigure l'avenir de toute une filière face aux défis de la transformation des compétences, de la productivité et de l'innovation permanente. Dans l'emballage comme ailleurs, la réussite sera collective.