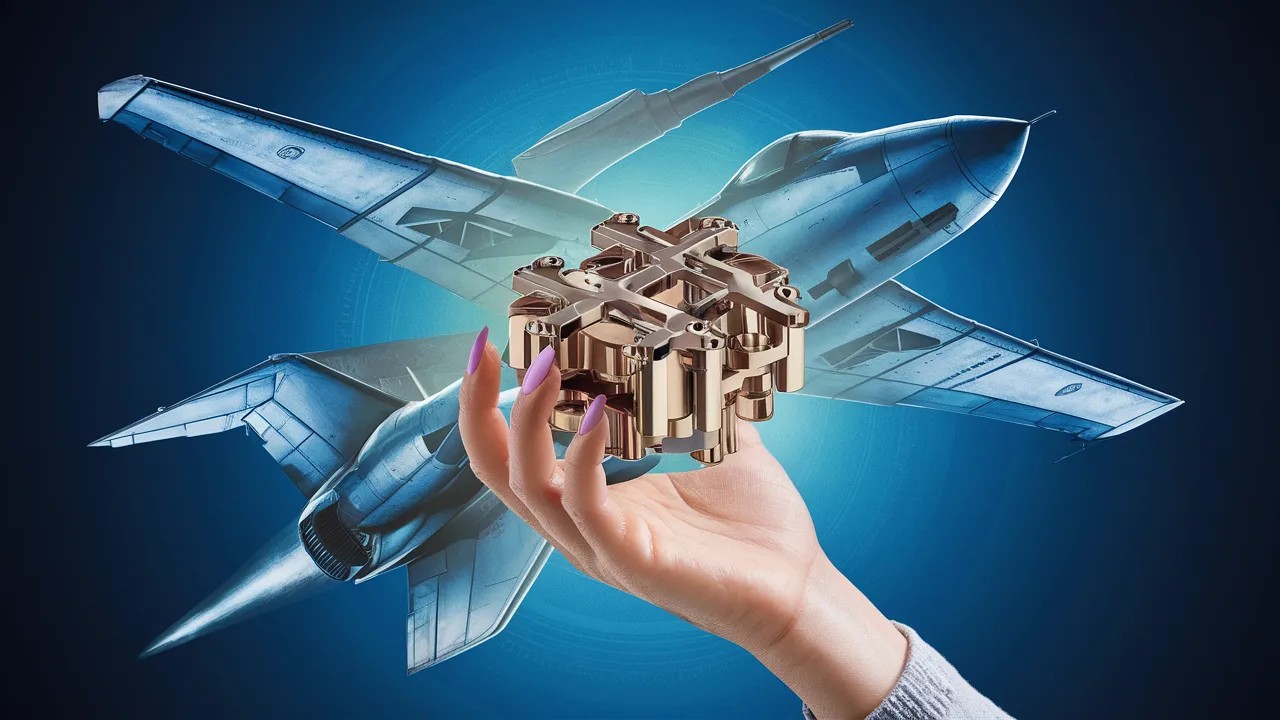
La fabrication additive révolutionne l’aérospatial
Imaginez des pièces d'avion ou de fusée aux formes complexes, dotées de cavités ou de structures en treillis, fabriquées couche après couche par une imprimante 3D. Ce qui relevait de la science-fiction il y a quelques années est désormais une réalité bien tangible dans l'industrie aérospatiale. La fabrication additive, ou impression 3D, a fait ses preuves et atteint une véritable maturité pour la production de pièces métalliques à haute valeur ajoutée.
Un long cheminement vers la qualification
L'adoption de la fabrication additive dans l'aéronautique et le spatial n'a pas été un long fleuve tranquille. Il a fallu de nombreuses années de R&D pour lever les freins, notamment liés aux enjeux de certification dans ces secteurs ultra-exigeants en termes de sécurité et de performance.
Il est impératif de démontrer que la qualité d'une pièce métallique issue de l'imprimante est équivalente à celle d'une pièce usinée.
– explique David Leutard, directeur des programmes du Safran Additive Manufacturing Campus
Grâce aux progrès technologiques, cet objectif est aujourd'hui atteint. Les pièces produites par fabrication additive affichent des performances mécaniques comparables à celles issues des procédés traditionnels. Elles sont même supérieures sur certains points, comme la possibilité de réaliser des géométries complexes optimisées.
Les technologies phares
Trois procédés se démarquent pour l'impression 3D métallique dans l'aérospatial :
- La fusion laser sur lit de poudre (L-PBF), considérée comme la plus mature, qui fait fondre sélectivement des poudres d'alliages à l'aide d'un laser.
- Le dépôt de filament fondu (FDM) qui utilise un filament chargé de poudre métallique et de liant, avec un post-traitement par frittage.
- Le dépôt de matière sous énergie concentrée (DED), technologie émergente permettant de fabriquer des pièces de grandes dimensions.
La société française Amfree, spin-off de l'Irepa Laser, s'est spécialisée dans le DED avec sa solution Clad-w. Grâce à l'utilisation d'un laser haute puissance, elle atteint des cadences jusqu'à 1000 cm3/h pour produire des pièces dépassant 2 mètres de diamètre.
De la pièce métallique à la céramique technique
Si les alliages métalliques constituent le cœur des applications aérospatiales, de nouveaux matériaux comme les céramiques techniques commencent aussi à être explorés. Leur stabilité thermique et chimique en fait des candidats prometteurs pour des environnements sévères comme les moteurs de fusée.
Le fabricant d'imprimantes 3D Pollen AM a ainsi créé une filiale dédiée aux céramiques techniques. L'objectif est de mettre au point des pièces capables de résister aux flux thermiques et d'éviter les problèmes de surchauffe ou de refroidissement.
Les grands projets en cours
Les acteurs du secteur multiplient les développements pour intégrer davantage la fabrication additive :
- Safran produit un support de palier pour turboréacteur dans son centre dédié à l'impression 3D.
- ArianeGroup travaille sur le moteur Prométhée qui utilisera des pièces imprimées en 3D, pour un premier vol prévu en 2025.
- Une imprimante FDM est actuellement testée en orbite dans la Station Spatiale Internationale.
Autant de projets qui illustrent la montée en puissance de la fabrication additive dans l'aérospatial. Cette technologie désormais mature ouvre de nouvelles possibilités de conception qui révolutionnent la façon de construire les aéronefs et les lanceurs. Un maillon essentiel pour préparer l'avenir de la conquête spatiale et de la mobilité aérienne.