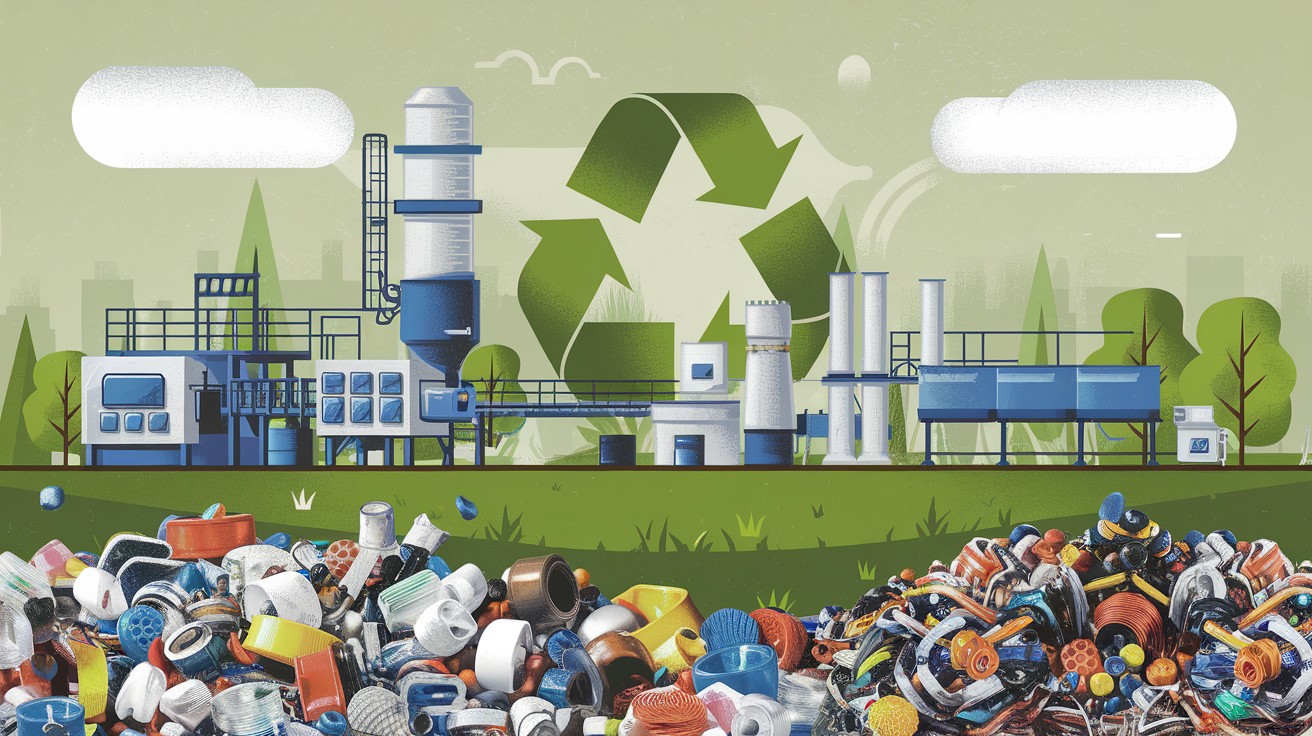
L’extrusion plastique se met au vert grâce au numérique
Face à l'urgence climatique, les industriels de la plasturgie n'ont d'autre choix que d'engager une profonde mutation écologique. Un défi de taille pour les acteurs de l'extrusion, procédé énergivore qui doit se réinventer pour réduire drastiquement son empreinte carbone. Heureusement, la transition numérique offre de précieux leviers pour relever ce challenge. Automatisation, pilotage intelligent, éco-conception... Focus sur une filière en pleine (r)évolution verte.
L'éco-conception, premier pas vers une extrusion durable
Avant même de repenser les process, les extrudeurs doivent commencer par éco-concevoir leurs produits. L'idée ? Intégrer les enjeux environnementaux dès la phase de développement grâce à l'analyse du cycle de vie (ACV). Cet outil permet d'évaluer les impacts d'un produit, de l'extraction des matières premières jusqu'à sa fin de vie.
"Nous sensibilisons fréquemment nos membres à ce volet qu'ils ont tendance à appréhender, de prime abord, comme un centre de coût et non comme une valeur ajoutée", souligne Yves Schmitt, directeur relations clients chez IPC. Le Centre technique industriel de la plasturgie propose d'ailleurs un outil d'ACV dédié baptisé C3R'Impact.
Cap sur les plastiques recyclés
L'éco-conception passe aussi par le choix de matières vertueuses comme les plastiques recyclés. Selon Yves Schmitt, "substituer un kilo de vierge par un kilo de recyclé permettrait de diviser par deux l'impact carbone". Des gains considérables malgré un coût encore supérieur de 30 à 40% par rapport aux résines vierges.
Un surcoût qu'il faut mettre en perspective avec les bénéfices environnementaux à long terme. C'est le pari de l'entreprise Silvadec, spécialiste des lames de terrasse en bois composite. Pour sécuriser son approvisionnement en plastique recyclé, ce fleuron breton a même investi dans sa propre usine de recyclage, qui produira 12 000 tonnes par an dès 2025.
Notre ambition est d'atteindre 100% de plastiques recyclés dans nos produits d'ici 2030.
Maël Thirion Vallette d'Osia, chef de projet Innovation chez Silvadec
La data au service de l'optimisation
Pour les extrudeurs, le passage aux matières recyclées implique de faire face à une plus grande variabilité. Un challenge technique que le numérique peut aider à relever. Pilotage intelligent, contrôles en ligne, maintenance prédictive... L'industrie 4.0 fournit de précieux outils pour maîtriser les process.
- Des capteurs pour suivre en temps réel les paramètres clés (température, pression, débit...)
- Des algorithmes d'auto-apprentissage pour optimiser les réglages
- Des jumeaux numériques pour tester virtuellement de nouveaux matériaux ou designs
Autant d'innovations qui permettent un pilotage plus fin et une meilleure réactivité. "Le numérique peut aider à stabiliser les process et à capitaliser sur l'expérience", résume Yves Schmitt. IPC planche d'ailleurs sur un logiciel baptisé SynQBox E, dédié à l'optimisation de l'extrusion.
Automatisation et montée en compétences
Au-delà des gains environnementaux, la digitalisation comporte un autre atout clé : faciliter le travail des opérateurs. Dans un contexte de pénurie de main d'œuvre, l'automatisation et les assistants numériques peuvent soulager les tâches répétitives. De quoi attirer de nouveaux talents en revalorisant les métiers.
"L'usine 4.0 permet de faire monter les collaborateurs en compétence, en s'appuyant sur leur expertise tout en leur fournissant des outils d'aide à la décision", analyse Yves Schmitt. Chez Silvadec, c'est tout l'enjeu du projet d'automatisation de la qualité en cours, qui vise à collecter et exploiter les données pour un pilotage optimisé.
Si le chemin vers une plasturgie décarbonée est encore long, la filière extrusion semble déterminée à prendre le virage. En combinant éco-conception, matériaux verts et technologies de pointe, ces industriels prouvent qu'écologie peut rimer avec compétitivité. Une mutation profonde portée par des pionniers engagés, avec le numérique comme accélérateur de la transition.