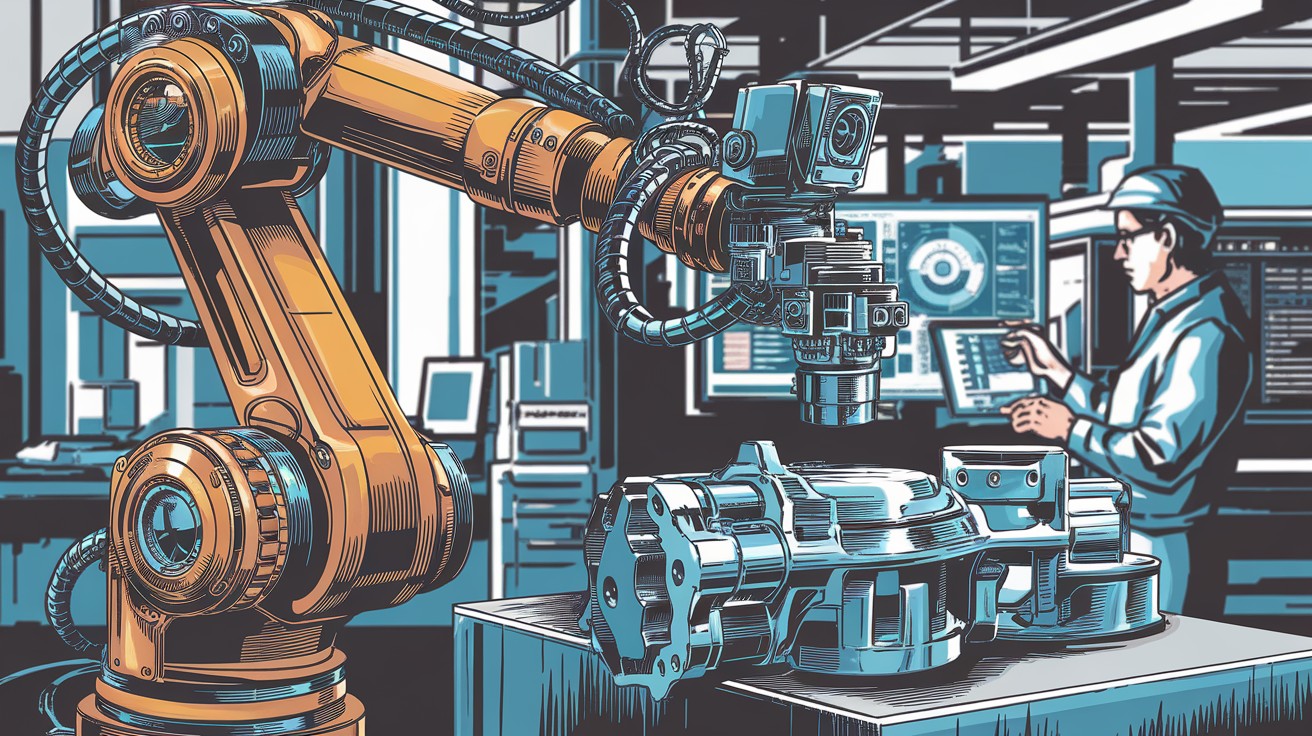
L’IA révolutionne le contrôle non destructif dans l’industrie
Imaginez un monde où les défauts les plus infimes dans les pièces mécaniques critiques seraient systématiquement détectés, où les inspections visuelles fastidieuses seraient confiées à des algorithmes ultra-performants. Ce monde est en train de voir le jour grâce à l'intelligence artificielle (IA) qui s'invite dans les ateliers de contrôle non destructif (CND). Une (r)évolution technologique qui promet des gains substantiels de productivité et de fiabilité pour les industriels de l'aéronautique, de l'automobile ou encore du nucléaire.
L'IA s'invite dans les méthodes CND traditionnelles
Historiquement, les contrôles non destructifs comme la magnétoscopie pour les matériaux ferromagnétiques ou le ressuage pour les matériaux non poreux reposaient sur l'expertise de techniciens qualifiés. Malgré leur savoir-faire, la variabilité humaine et la fatigue visuelle lors des inspections répétitives constituaient des facteurs de risque pour la fiabilité des contrôles. C'est là que l'IA entre en scène pour automatiser l'analyse des indications et assister les opérateurs.
Yannick Mafille, ingénieur CND au Cetim, souligne l'intérêt particulier de l'IA pour les industriels inspectant des grandes séries :
L'utilisation de l'IA est particulièrement pertinente lorsqu'il faut inspecter des milliers de pièces par jour comme dans l'industrie automobile ou le traitement de surfaces.
Yannick Mafille, ingénieur CND, Cetim
Son équipe a ainsi développé le démonstrateur MAIA (Magnétoscopie assistée par intelligence artificielle) qui met en évidence le potentiel de l'IA pour la détection automatisée de défauts sur des pièces forgées.
Des algorithmes entraînés pour détecter l'invisible
Le nerf de la guerre de l'IA réside dans la donnée. Pour entraîner les algorithmes de vision par ordinateur, les ingénieurs du Cetim ont constitué une base de plus de 5 000 images de défauts détectés par magnétoscopie fluorescente sur près de 500 pièces forgées comme des bielles, des vilebrequins ou des tulipes de transmission.
Une fois correctement entraînés, les algorithmes deviennent alors capables de détecter automatiquement et avec une grande fiabilité les fissures, les tapures ou autres défauts difficilement perceptibles à l'œil nu. Un gain de temps et de répétabilité considérable pour les opérateurs CND.
Vers des inspections CND augmentées
Au delà de la détection, l'IA ouvre la voie à de véritables inspections augmentées où les données des différents capteurs (ultrasons, courants de Foucault, thermographie…) sont agrégées et analysées pour fournir un diagnostic complet de l'état de santé des pièces.
Le projet collaboratif FANTOM (Flexible and Automated NDT Plateform For Manufacturing), piloté par l'IRT Jules Verne, développe ainsi une plateforme robotisée flexible intégrant des briques d'intelligence artificielle pour l'inspection de pièces aéronautiques composites de grandes dimensions.
L'IA s'attaque à toute la gamme des CND
Si les premiers cas d'usage concernent principalement la magnétoscopie et le ressuage, l'IA a vocation à se déployer sur l'ensemble des méthodes de CND :
- Analyse automatisée des images de radioscopie numérique
- Détection de défauts par thermographie infrarouge
- Caractérisation des indications ultrasons multiéléments
- Traitement des données massives issues de la tomographie
Les industriels l'ont bien compris, à l'image de ZNCI IDF qui a investi 1,50 M€ dans une nouvelle machine de contrôle multi-éléments pour les pièces moteurs d'avion.
Gageons que d'ici quelques années, l'intelligence artificielle aura investi tous les ateliers CND, pour le plus grand bénéfice de la qualité et de la sécurité des produits industriels. Une révolution technologique à laquelle le Cetim compte bien contribuer en accompagnant les entreprises dans l'intégration de ces nouvelles solutions.